Turck offers
intelligent bus stations, with built-in bus electronics, interface with
your existing devices. TURCK bus stations provide diagnostics, short
circuit protection, automatic baud rate detection, and are node
addressable.

AS Interface
Systems
AS-interface (commonly referred
to as AS-I) is a low-level I/O system. It was originally intended
to be a simple, low cost system that would be easy to install and
maintain. With that philosophy in mind, the original developers
designed AS-I as a discrete-only two wire system. It incorporated
features like automatic station addressing, and power and data
were carried on a single untwisted pair of wires. Today.
AS-I can be used as a stand alone network or can be connected to a
higher level system, such as DeviceNet, or Profibus-DP, through a
gateway. The gateway acts as a slave to the higher system and a
master to the AS-I system
-
Cordsets
-
Bulk
Cable
-
I/O
Products
-
Interconnect
Products
-
Masters
-
Safety
-
Accessories
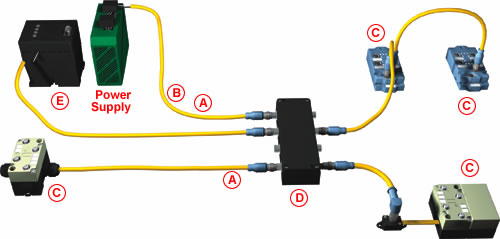
|
CANopen Systems
CANopen is a higher-layer system based on
the CAN (controller area network) specification that defines device and
communication profiles. Device profiles standardize the data content of the
various supported device types, while communication profiles determine the
method of data exchange between the devices. The basic communication methods
are real time data (process data objects – PDO) and parameter data (service
data objects – SDO).
-
Cordsets
-
Bulk
Cable
-
I/O
Products
-
Interconnect
Products
-
Accessories

|
DeviceNet
Systems
DeviceNet is a low-cost
communications protocol that eliminates hard wiring and connects
industrial devices such as limit switches, photoelectric
sensors, valve manifolds, motor starters, process sensors, bar
code readers, variable frequency drives, panel displays and
operator interfaces to a network. DeviceNet’s direct
connection provides improved communication between devices, as
well as important device-level diagnostics not easily accessible
or available through hard-wired I/O interfaces.
-
Cordsets
-
Bulk
Cable
-
I/O
Products
-
Interconnect
Products
-
Accessories

|
Ethernet / Profinet Systems
Ethernet is the most popular
protocol used to connect office computers and peripherals today.
It is increasingly findings its way into other applications, and
is rapidly becoming the network of choice for higher level
industrial control applications. Ethernet is primarily used to
connect PLC’s, computers, HMI displays and other high level
components.
-
Cordsets
-
Bulk
Cable
-
I/O
Products
-
Interconnect
Products
-
Accessories

|
Foundation Fieldbus Systems
Foundation fieldbus is a
communications protocol and physical method to interconnect
smart devices such as temperature transmitters, pressure
transmitters and valve actuators. The physical layer conforms to
ISA SP50.02 and IEC 1158-2 standards for fieldbus. Fieldbus
technology allows many smart devices to share one communication
medium. The digital communication signal is superimposed onto a
DC carrier. This reduces the amount of terminations to connect
all the field devices to a host system and allows greater
flexibility for future additions of I/O points.
-
Cordsets
-
Bulk
Cable
-
Interconnect
Products
-
Power
Conditioners / Supplies
-
Accessories
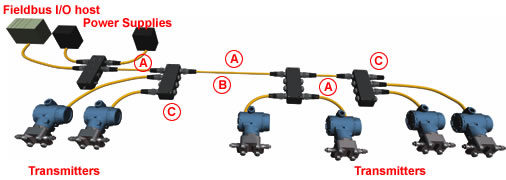
|
HART Systems
HART (Highway Addressable
Remote Transducer) provides digital communication to
microprocessor-based (smart) analog process control instruments.
Originally intended to allow convenient calibration, range
adjustment, damping adjustment, etc. of analog process
transmitters; it was the first bi-directional digital
communication scheme for process transmitters that didn't
disturb the analog signal. HART has since been extended to
process receivers, and is sometimes also used in data
acquisition and control. HART specifications continue to
be updated to broaden the range of HART applications.
HART was developed in the
early 1980s by Rosemount Inc. Later, Rosemount made it an
open standard. As the de-facto standard for data
communication in smart analog field instruments, HART is found
in applications ranging from oil pipelines to pulp and paper
mills to public utilities. Among the many HART products
now available are:
- Analog Process
Transmitters
- Digital-only Process
Transmitters
- Multi-variable
Process Transmitters
- Process Receivers
(Valves)
- Local (Field)
Controllers
- HART-to-Analog
Converters
- Modems, Interfaces,
and Gateways
- HART-compatible
Intrinsic Safety Barriers
- HART-compatible
Isolators
- Calibrators
- Software Packages
|
Profibus-DP Systems
Profibus-DP is an industrial
network protocol that connects field I/O devices in order to
eliminate hard wiring. The network connection increases
device-level diagnostic capabilities, while also providing
high-speed communication between devices.
-
Cordsets
-
Bulk
Cable
-
I/O
Products
-
Interconnect
Products
-
Accessories

|
Profibus-PA Systems
Profibus-PA (Process
Automation) uses synchronous transfer mode technology, as
defined in IEC 61158-2, to communicate between field
devices and the RS 485 backbone of Profibus-DP. A segment
coupler, or gateway is installed to bridge profibus-DP with
Profibus-PA. Otherwise, the protocols are identical, allowing
transparent communication between general purpose automation
systems and decentralized field devices.
-
Cordsets
-
Bulk
Cable
-
I/O
Products
-
Interconnect
Products
-
Accessories
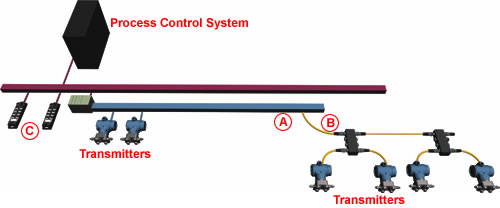
|
SDS Systems
The Smart
Distributed System, developed by Honeywell's MICRO SWITCH
Division, is a bus system for intelligent sensors and
actuators. The SDS system is based on CAN as defined in the
Bosch V2.0 CAN Specification. SDS allows multiple nodes
to share a single bus. Over a single 4-wire cable, Smart
Distributed System can interface up to 64 nodes with a maximum
of 126 addresses. These intelligent sensor and actuator devices
do more than just turn on and off. Smart Distributed System
devices have advanced
device-level functions, system and device diagnostics. SDS
is based on a three layer communication model. The Application
Layer specifies system services and protocol. The
Data Link Layer provides functions and procedures to establish,
maintain and release data-link-connections among devices on the
network and to transfer data-link-service-data-units. The
Physical Layer provides the mechanical, electrical, functional
and procedural means to activate, maintain and de-activate
physical connections for bit transmission between
data-link-entities. Physical Layer devices are interconnected by
physical media. |
|